TPSの原点:メインラインはお客さまによって動く
- Hatsuo Yamada
- 2022年3月4日
- 読了時間: 3分
計画より多い部品は、異常としてすぐに発見されます。
計画の数量より増えてしまった20個分の在庫は、メーカーさんの出荷場や輸送中のトラック、ラインサイドの棚に入りきれなくなってしまいます。置き場も最初の計画で全て決まっていますので、20個分の部品の置き場はありません。
余った2パレットが所定の場所に保管しきれなくなりますから、メーカーさんの出荷場や輸送中のトラック、ラインサイドの棚の近辺を見れば、どこかに余っているはずです。
輸送中も含めて保管する場所は、上記の3ヶ所で、それぞれ2パレットと、手持ち分が決まっています。
ラインサイドの棚に入りきれなくなってしまったパレットは、他に行き場所がありませんから、取り敢えずその部品棚の付近に置かれることになります。所定外の場所に部品が放置されていたら、すぐに「おかしいな?」と気が付きます。異常が起きていることを目で見て知ることができる仕組みです。
ルームミラーのパレットが2つ置き場所がないという現象に気づいたら、「カンバン」を2枚多く流通してしまったことがわかりますので、まず2枚をの「カンバン」を回収して、流通させなくします。
その上で、なぜ誤って2枚の「カンバン」が流通してしまったのかを突き止めます。「なぜだ?なぜだ?」とやるわけです。原因が見つかったら、その原因を取り去ることで、初めてこの問題は解決となります。
「カンバン」はJITという考え方を具体的に進めるための、代表的なツールの一つであることは説明しました。「カンバン」一つをとってもこのように結構深い意味があります。
次にJIT全体のイメージを説明します。みなさん大きな川が流れているところをイメージしてください。生産ラインは上流から下流に大きな川のような流れとなっています。
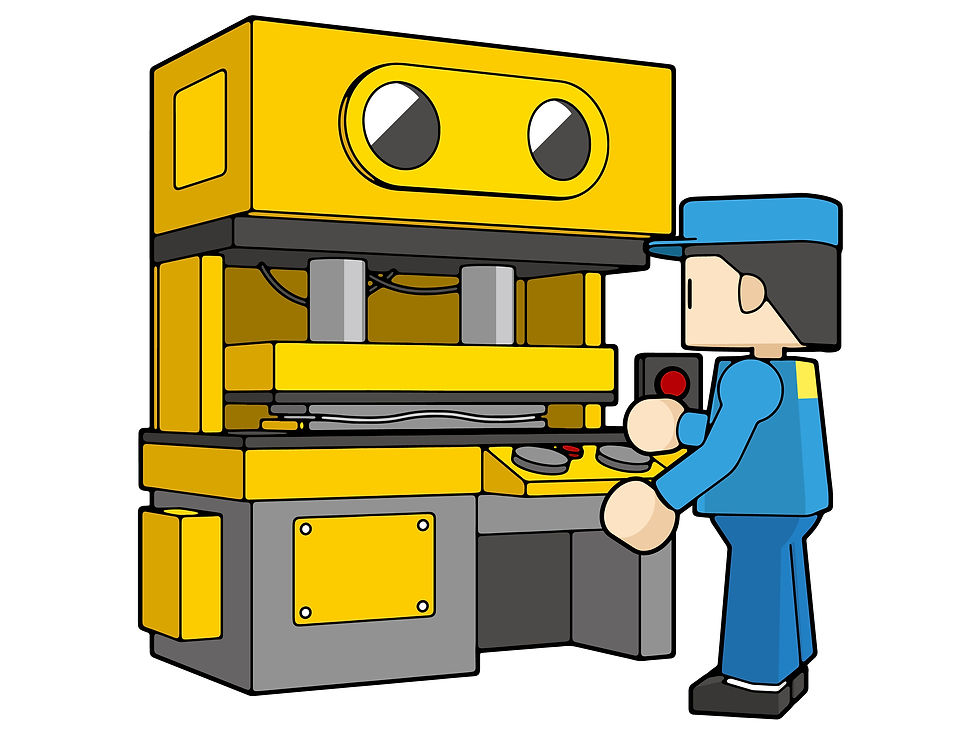
この流れの源流は、プレスされた鉄板から始まります。車の床(フロアー)、天井(ルーフ)、両側のパネル(サイドメンバー)の3つ流れが一つになり、ホワイトボデーと呼ばれる車の骨格が出来上がります。
そこへ、ドアやボンネット(フード)、トランク(ラッゲージ)の蓋などが付けられます。
その後ホワイトボデーは塗装され、組み立て工程で様々な部品が取り付けられます。
組み立て工程では先ほど例に挙げたルームミラーをはじめ、タイヤ、シート、ダッシュボード(インストルメンタルパネル)などが、組み付けられますが、これらは、いわば、川の支流に当たります。
大きな川に注ぐ支流を、思い浮かべてみてください。
コンベアに乗って流れていく塗装されたボデーが本流に流れています。支流から本流へ、さまざまな部品が合流します。決められたタイミングで、組み付けられていきます。
ここまでの流れは全て、タイミングが決まっています。正確に何時何分何秒にルームミラーを組み付けるというタイムテーブルがあるわけではありません。
しかし、先ほど説明した、「カンバン」によって、60個のルームミラーが所定の場所に順番に従って待機しています。同期した状態になっているイメージを掴んでいただけたでしょうか。
この流れは、何の力で動いているのか?と言いますと、「ベルトコンベアを駆動するモーターじゃないの?」という答えが返ってきそうですが、実は「お客さま」なのです。
「私も車を持っているけど、車の製造ラインを動かした覚えはないよ!」と、ほとんどのお客様はおっしゃると思いますが、「お客様が1台購入してくださった」という情報が、最終工程から流れの源流である、製造ラインのプレス工程にまで伝播していき、プレス工程では新しい部品をプレスし始めます。
「お客さま」が1台の車を購入して下さることが、製造ラインを動かしているということができるのです。スマートな言い方をさせていただけば、バリューチェーンということになると思います。
Comments