Origin of TPS: The mainline is driven by the customer.
- Hatsuo Yamada
- Mar 4, 2022
- 3 min read
More parts than planned are quickly discovered as anomalies.
The inventory of 20 pieces, which has increased from the planned quantity, will not fit in the manufacturer's shipping area, trucks in transit, and lineside shelves. In addition, there is no storage space for 20 parts because the storage space is all decided in the initial plan.
The extra two pallets can no longer be stored in the designated place, so if you look at the manufacturer's shipping area, the truck being transported, or the lineside shelves, there should be some extra.
There are two pallets for each of the above three places to store, including during the championship. And the amount you have is decided.
For example, a pallet that can't fit on the lineside shelf has no other place to go. So they will place near the parts shelf for the time being. If a part is left in an unspecified place, you will immediately notice "is it strange?" It is a mechanism that allows you to know that an abnormality has occurred visually.
If you notice the phenomenon of two extra pallets in the rearview mirror, you can see that two more "Kanban" have been distributed, so first, collect the two "Kanban" and stop distributing them.
Then, find out why the two "Kanban" were accidentally distributed. "Why? Why?" Once the cause is found, removing the cause will only solve this problem.
I explained that "Kanban" is one of the representative tools for concretely advancing the idea of JIT. "Kanban" has such a deep meaning.
Next, I will explain the image of the entire JIT. Imagine a big river flowing through you. The production line flows like a big river from upstream to downstream.
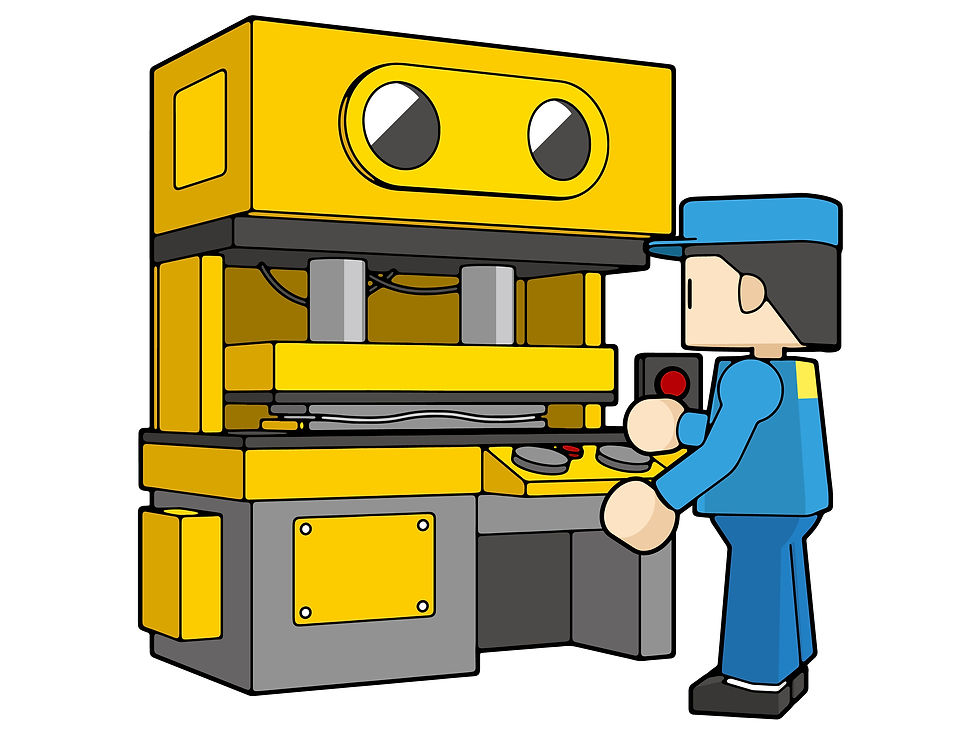
The source of this flow begins with the pressed iron plate. Next, the three streams of the car floor, ceiling, and panels on both sides (side members) are combined into one, creating a car skeleton called a white body.
Doors, hoods, trunk lids, etc., can be attached.
The white body is then painted, and various parts are attached during the assembly process.
In the assembly process, the rearview mirror mentioned earlier, tires, seats, dashboard (instrumental panel), etc., are assembled, but these are tributaries of the river.
Imagine a tributary that flows into a large river.
The painted body that flows on the conveyor is flowing in the mainstream. Various parts merge from the tributary to the mainstream. They will assemble at fixed timing.
The timing of all the steps up to this point is fixed. There is no timetable to assemble the rearview mirror precisely at what hour, minute, and second.
However, due to the "Kanban" explained earlier, 60 rearview mirrors are waiting in order in place. Could you grab the image that is in sync?
What is the force behind this flow? The answer seems to be, "Isn't it the motor that drives the conveyor belt?", But it's a "customer."
Most customers say, "I own a car, but I don't remember moving the car production line!", But the information that "the customer bought one" is It propagates from the final process to the pressing process of the production line, which is the source of the flow. In the pressing process, new parts are started to be pressed.
It can be said that the fact that the "customer" purchases one car drives the production line. To put it smartly, I think it's a value chain.
コメント