"Eternal Challenge" created by Scotoma.
- Hatsuo Yamada
- Apr 4, 2022
- 3 min read
Updated: May 29, 2022
March was a milestone in the Kaizen activities that I support. Some announcements of the results reported the emergence of improvement activities.
As an engineer, every engineer naturally has the desire to "create a good product."
The team introduced this time has been a top runner so far.
It's a bit of a stumbling block right now, but I think they'll be ready to move on to the next stage.
From the start of product development, we have introduced cost planning.
There are many competitors for new products, and to show their presence there, we aimed to reduce costs and secure overwhelming competitiveness by drastically changing the structure of the products.
In the early stages of conception, they devised an unprecedented structure, and I felt like I was able to take a breather.
However, when I evaluated the prototype, I found 4 to 5 problems and crushed them one by one, but I could not overcome the last problem.
So they decided to postpone it for a year and got full approval.
As for technical matters, I am an outsider and have no opinion, but I also measured the task's difficulty. Toyota has never experienced such a thing.
In parallel with this activity, I had the opportunity to talk with someone who had experience as a Toyota CE (Chief Engineer).
Before meeting him, I had a few years of doubts about set-based concurrent engineering in Lean product development. So I took this opportunity to ask him this question.
With one word, "I don't understand what Mr Yamada is saying," I quickly resolved the question.
Let me explain a little more concretely. In Toyota's product development, we will summarize the concept of the CE concept while playing catch with related parties in advance.
Each expert picked up the feasibility and improvement plans and incorporated them into the CE concept at this stage.
Therefore, even if an unexpected problem occurs after the evaluation, it is customary and commonplace to solve the problem with the stance that "it must be established".
The method used at this time is "Toyota's problem solving".
The problem is solved by bridging the gap between what it should be (concept here) and the current situation (test results).
"Why why five why" is the main engine for solving this problem.
I expect that the content will be a little more advanced than the reason why the cause analysis of the quality defect problem.
He says, "Everyone is trying to solve problems regularly, so we will develop a solution that everyone involved can understand."
I think this is "preparing for them to move on to the next stage," so I would like to use this technique and work together to find a solution.
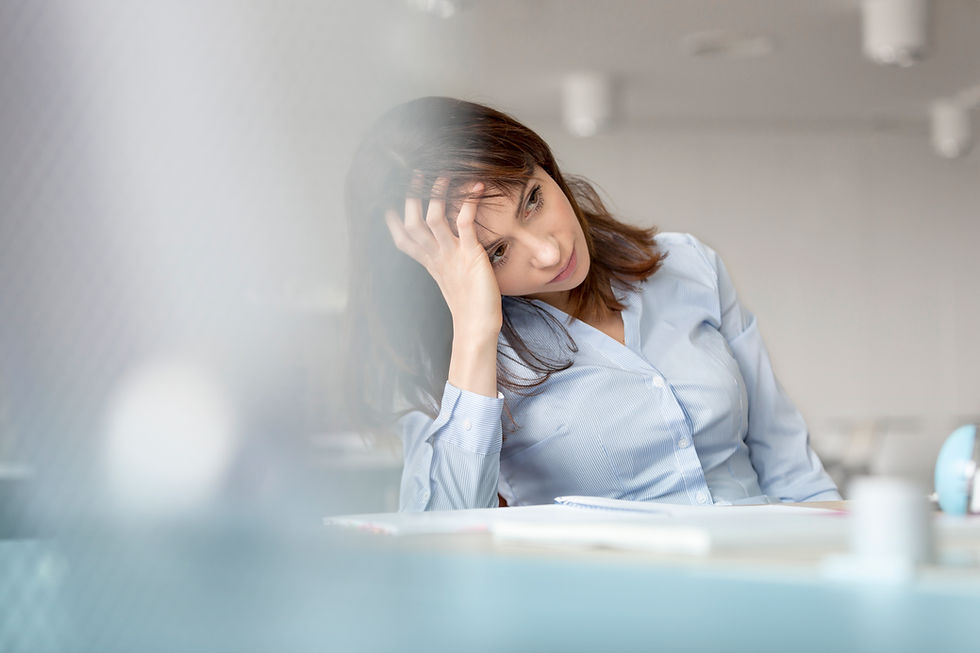
よく「永遠の課題」などという言葉を使う人がいます。しかし、真剣に取り組めば、そんなものはあるはずが無いのです。
「永遠の課題」にしてしまうのは、今は断言しませんが、その組織に根付いてしまったスコトーマ(心理的盲点・・トヨタ式では思い込みです)の仕業だと思います。
諦めないことは基本です。諦めたら解決できる問題も解決できるわけがありません。
解決策は必ず見つかります。
「永遠の課題」に終止符を打って、次の大きな課題にチャレンジしてもらいたいと考えています。
これも、カイゼンの1種ですので、
「あるべき姿=3ヶ月程度で課題を解決する」とし、現状わかっていることを見える化することから初めて、スコトーマをトーマを見える化する事から始めていきたいと考えています。
Comments