Daily management 7 / Own process completion ③
- Hatsuo Yamada
- Oct 13, 2022
- 2 min read
In everyday work, it is fundamental to allow workers to judge whether the process is good or bad.
In self-process completion, it is the same whether the work quality meets the requirements of the post-process.
It will be the criteria for judgment.
We call it the "Quality Condition".
If you proceed with kaizen using the concept of self-process completion, you will find information and data that are not used by subsequent processes.
It is an example often used to explain when promoting self-process completion activities.
A conversation between a stationery purchaser and his boss.
Boss: "When do you order notebooks?"
"It looks like it's a little accumulated."
Person in charge: "We purchase 30 books at the end of every month."
Boss: "What?
Person in charge: "(Confidently) Yes, I'm doing what my senior told me to take over!"
boss "·····"
It sounds like a joke, but there are surprisingly many such cases.
It was everyday work that hadn't been reviewed in years.
Maybe when my senior was doing it before, I didn't pay much attention to the cost,
I think it started with the condition that the person in charge would not have to worry about not having a notebook when they wanted to use it.
However, we didn't see it as abnormal and it didn't improve.
It would have been nice to change the standard to "I will place an order when the inventory reaches 2 (because the delivery lead time is 2 days)", but PDDDDDDDDD instead of PDCA...
When my boss finds out about this, I sometimes say, "Huh? Did you do that?"

The important thing is that the following management goes around.
①Raise your hand if there is an abnormality (an announcement will come).
②The leader provides emergency treatment on the spot of abnormal measures.
②Permanent measures to identify and eliminate the cause.
③Once the problem is solved, rewrite the standard document (revision of the standard document)
If there are no abnormalities, work will flow autonomously.
The person in charge can be confident that what they are doing is beneficial for the post-process and, in turn, leads to customer satisfaction.
This error handling and permanent countermeasure are the same as the mechanism of "ANDON" at the manufacturing site.
When the worker finds an abnormality, they pull the Andon string and notify the manager of the abnormality.
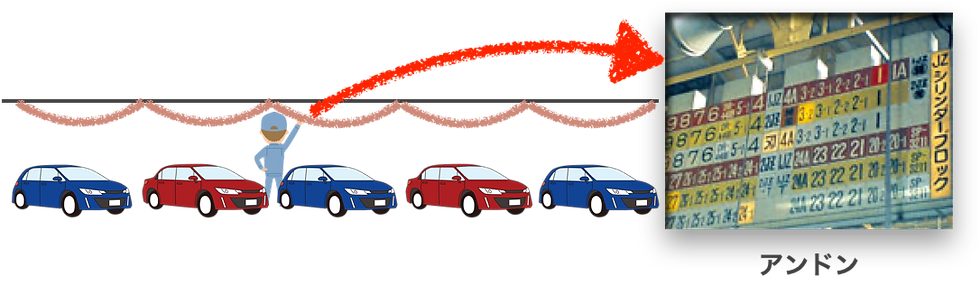
ANDON
Furthermore, we can trace back to the mechanism that Old Sakichi built into the Toyota automatic loom, which automatically stops the machine when the yarn breaks (abnormal).
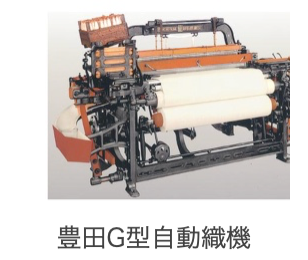
Toyota G-type automatic loom
Comentários